Welcome to the Rare Woods USA Woodworker Sessions interview series. Here, we hope to discover more about what makes our woodworkers tick, how you became involved in the craft, how and why you build your pieces and maybe learn a few secret techniques and tips along the way!
Our interviewer, a woodworker since the age of 8, Tobias Lochner is no stranger to the workshop. Find out more about him here.
Mark Donovan of Bowdoinham, Maine is our 11th Woodworker Sessions USA interviewee! We hope that you enjoy his story…
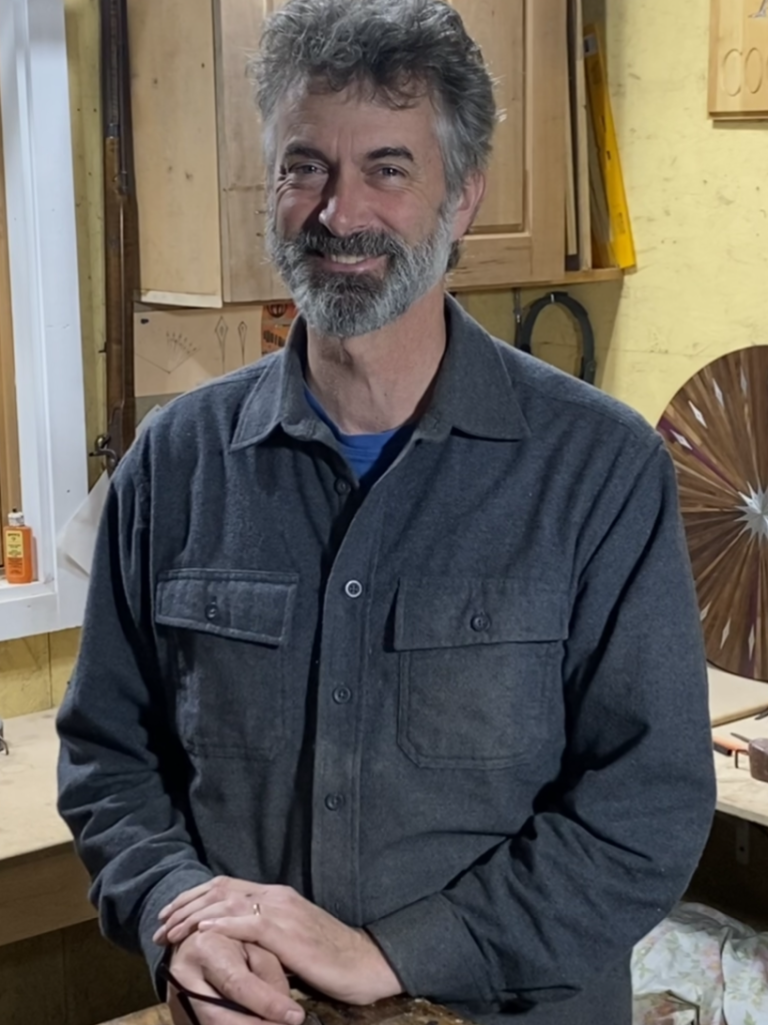
Question #1
Tobias: Hi Mark. Please tell us a bit about yourself, what is/was your career, a little about your family and how you became a woodworker.
Mark: I live in Bowdoinham in Maine, a small rural town on the Northeast end of Merrymeeting Bay. It is not far from my parents’ home, so I can say that I have lived in the mid-coast area most of my life. My wife Brigid and I built our home here almost 30 years ago. We raised two sons, Michael and Matthew, who are now beginning their own adult lives. We have also enjoyed being parents to Golden Retrievers and we have had six since living here in Bowdoinham.
I began my career in Infornmation Technology as a Systems Analyst for two major companies in the mid-coast area. Although the work was challenging and paid very well, I struggled with a sense of accomplishment. The business areas that we supported often moved so fast that it was hard to provide timely solutions and make the business clients happy. I felt that I needed to create more tangible and permanent products for my efforts.
After our first child was born, Brigid and I decided that she would return to work in IT (she is much better at it than I was) and I would stay at home with our son. It was then that we decied to convert an outbuilding into a woodshop, where I could work from home.
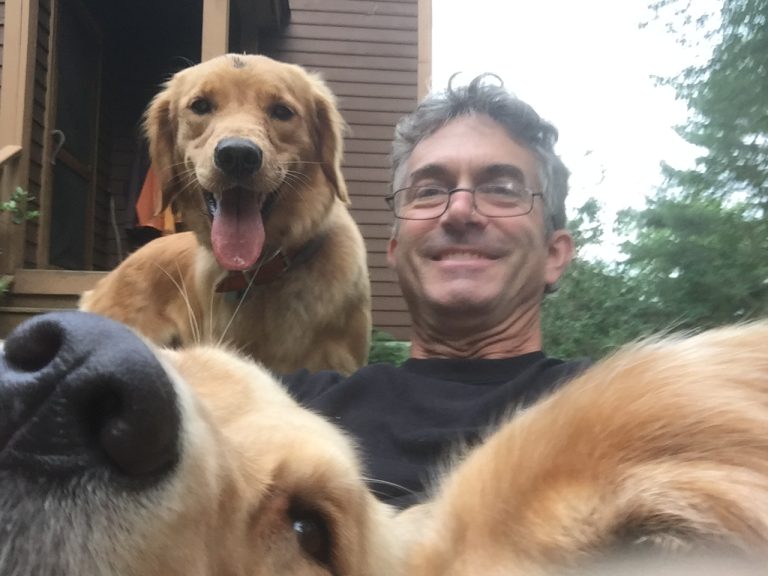
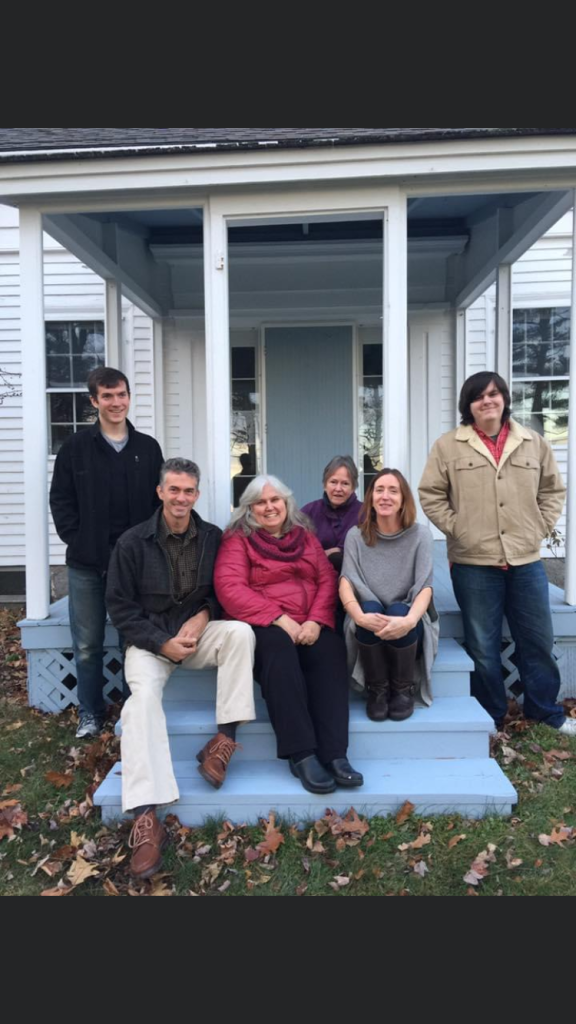
Question #2
Tobias: How did you get started doing woodwork and how long have you been a woodworker?
Mark: I guess that I have always been a woodworker, but it took a very long time for me to become competent enough to call myself that. Growing up on Westport Island, I didn’t have many outlets for entertainment. I would end up in the barn where there was lots of wood in the loft and some hand tools on the workbench that I was allowed to use. I remember finding a rasp that I could create shapes with, instead of just straight cuts. What a discovery!
My grandfather Jay Hanna, was a professional woodcarver and modelmaker. I remember his shop well. I loved the smell of the room as the door opened. I loved the walls lined with different kinds on wood, all shapes and sizes. I loved the sense of unlimited possibilities with all the tools at the ready.
In my senior year at high school, I was allowed to deviate from my class schedule and attend the Industrial Arts program, where I took metalshop and woodshop classes. This was the first time that I received formal instruction and I loved it. I have been working professionally in my own shop for over twenty years now.
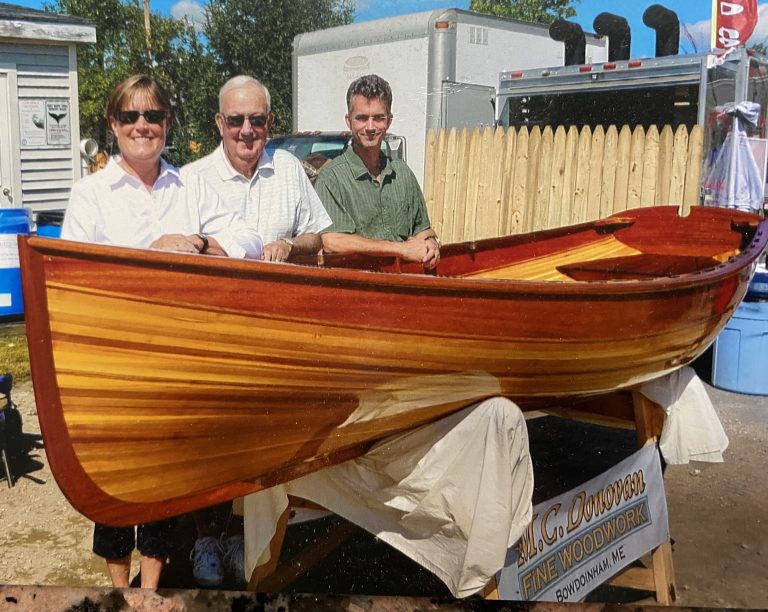
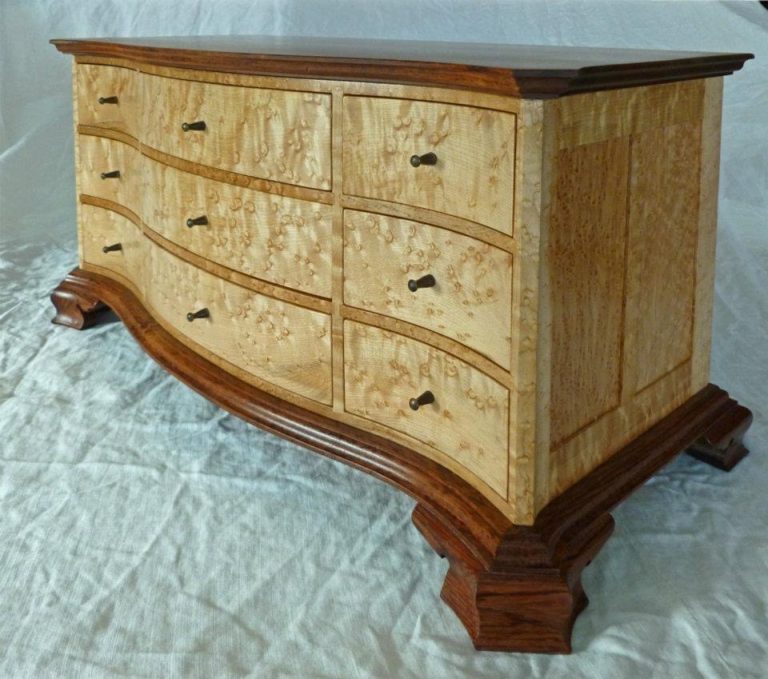
Question #3
Tobias: What was the first item you ever made and which is your favorite piece?
Mark: I attempted many pieces in my earlier years, but they were crude, showing my lack of experience and patience. Flashback to when I was 10 or 12, I asked my grandfather if he would make one of his traditional eagle carvings for me someday. He told me “No, you will have to make your own”.
Being young, I couldn’t understand how this was possible, and didn’t try. The day he passed away, I left work early and went home to grieve and began carving his pattern. I realized only then that he was right, and that this was the only way I could have one now. It was the first time that I exercised the patience, the care and the absolute best of my ability in the moment. So I will say that carving was my first attempt at a quality piece.
My favorite work to date is a pair of mahogany doors that I carved in 2008. The owner asked if I could carve butterfly bushes (Buddleia davidii), as they were to be planted on either side of these entrance doors. I confessed that I had no idea, as I had never done anything like that before. So I made a test panel, proposed a design and I got the job! I get to visit the doors every year to clean and oil the Mahogany, an experience that I enjoy immensely.
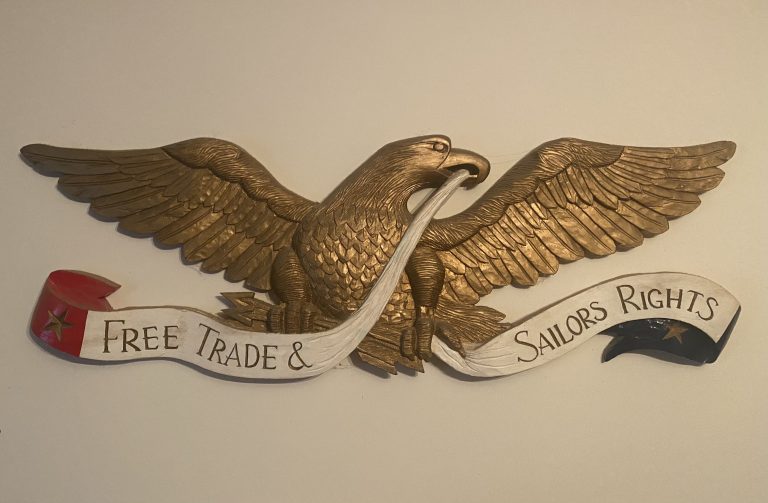
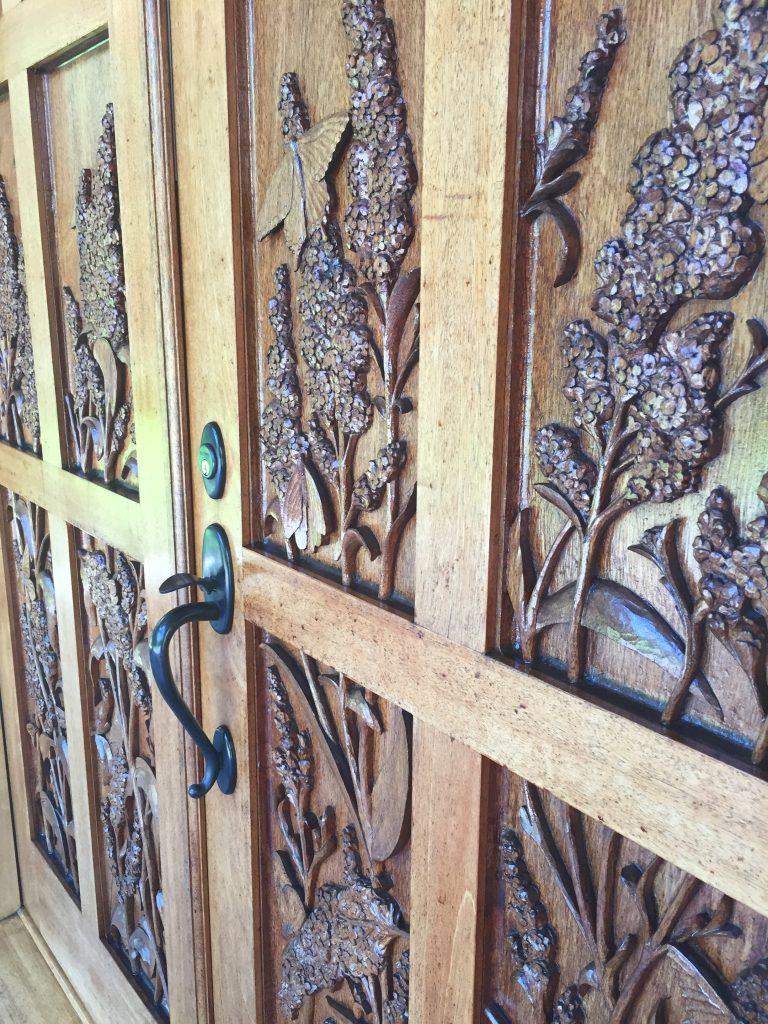
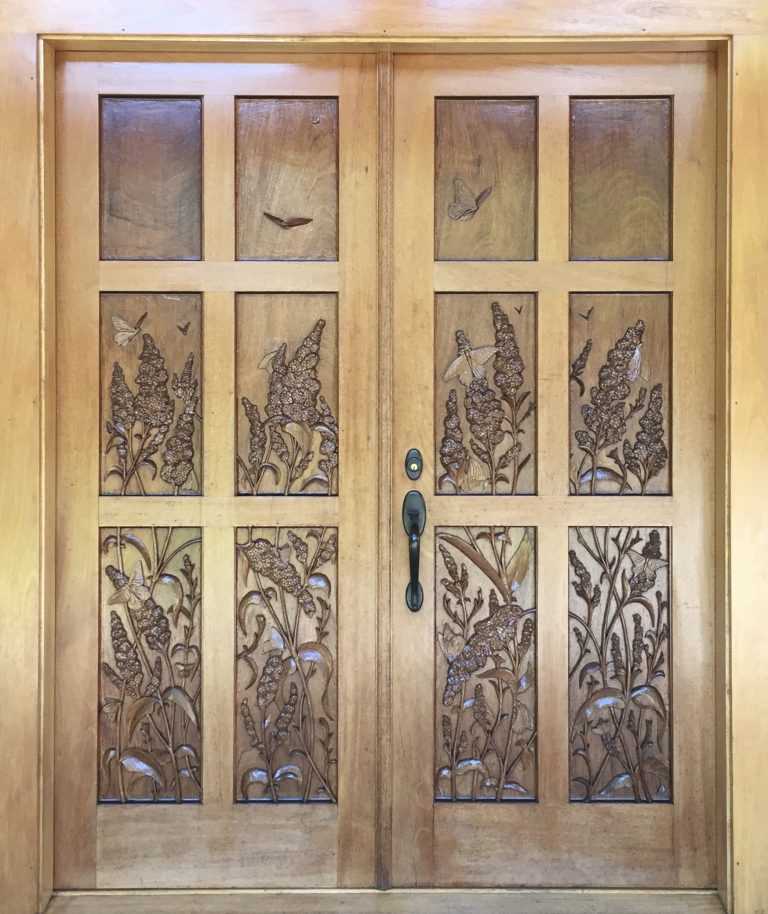
Question #4
Tobias: Which style of furniture do you enjoy building the most?
Mark: I like the clean and simple lines of Arts & Crafts, the Craftsman styles of Morris and Stickley, as well as the fluid chairs of Sam Maloof and the natural slabs of Nakashima. I am also drawn to the Danish furniture now referred to as Mid-Century-Modern. I feel that these styles have influenced the pieces that I have made.
I currently like designing and building standing height occasional tables with an organic aesthetic. Table tops also provide the perfect opportunity to displayinteresting grain and figure or inlays, to make the table a piece of functional artwork.
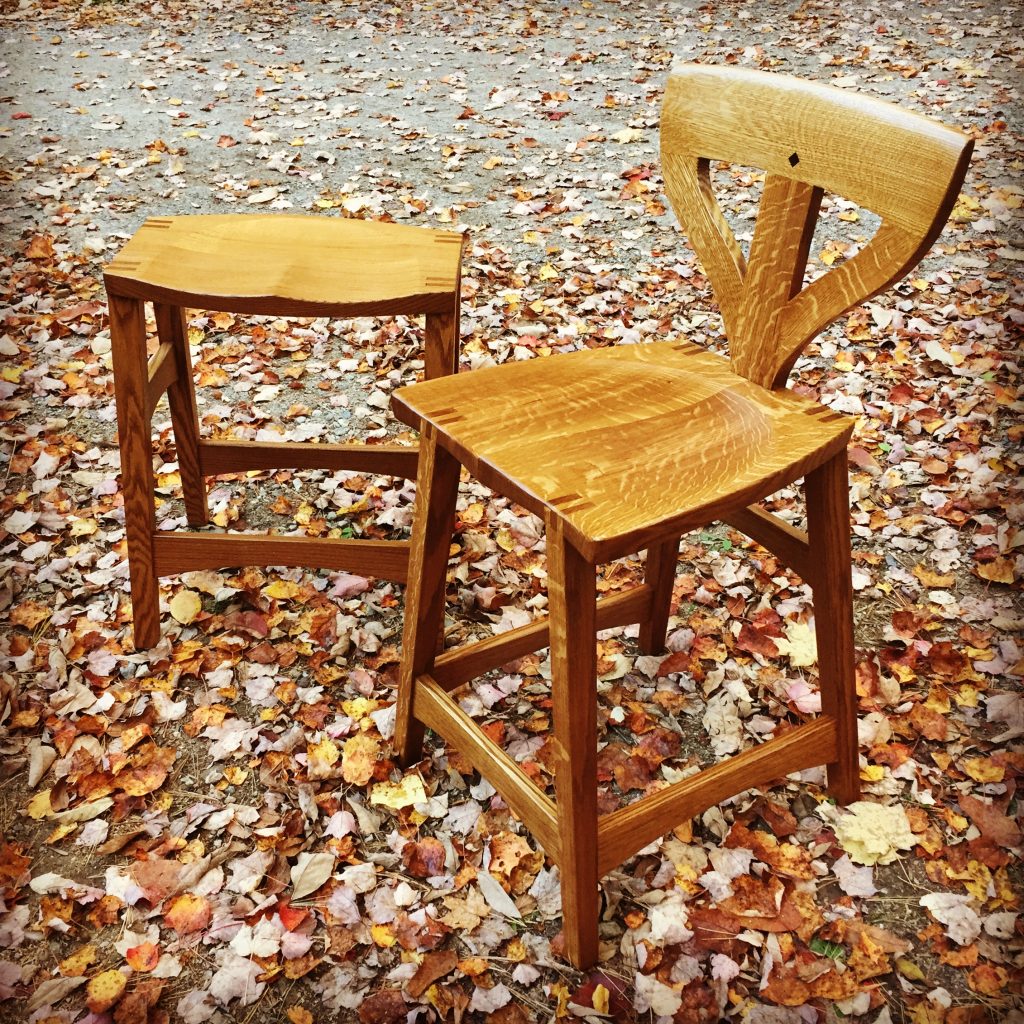
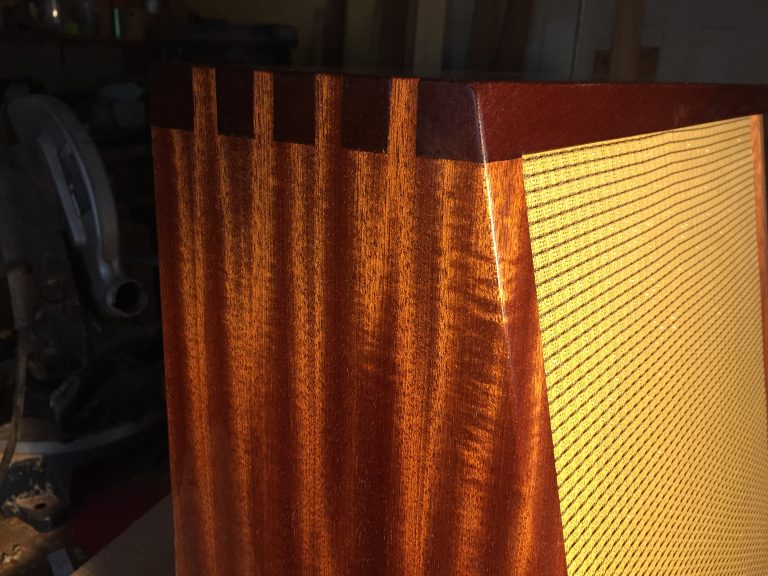
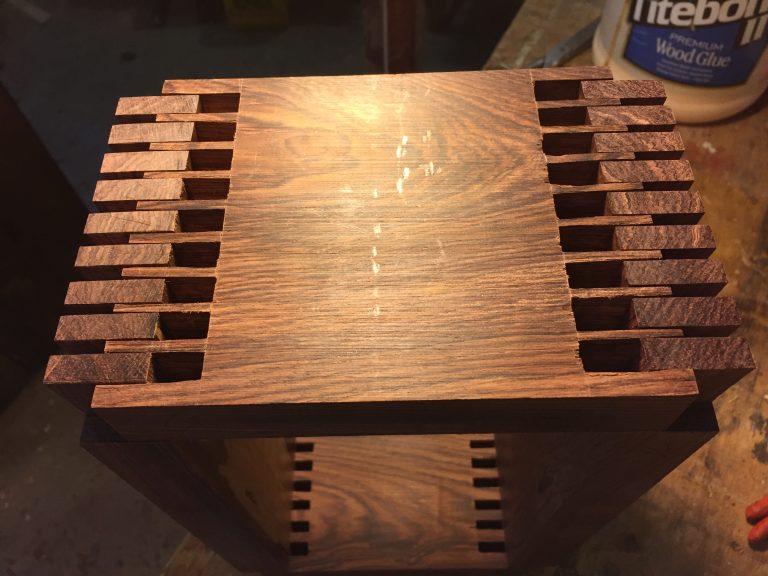
Question #5
Tobias: Which are your favorite local lumber species and which are your favorite exotics to work with?
Mark: This question is easy, I am a fool for figured Maple! Where I live, there are several species of Maple that are local and plentiful. I always keep an eye open for curly and birdseye figure in the lumber yards and in felled trees. My favorite ones are those that I discover on my own! Brigid often jokes that I have left tyre marks in the road while stopping to look at a log left on the ground. A few years ago, I salvaged a Hard Maple tree trunk that was abandoned on a property not far from my house. I contacted the owner and he was happy to have me remove it. It had a small piece of bark missing where I could see some unusual grain, so I had a hunch that it would be well worth the effort. When I began to cut it up, the side grain revealed a magnificently burled and twisted figure, visible even through the rough chainsawn surface.
I also like working with very hard and dense exotics like Rosewood, Ebony and Purpleheart. I enjoy how clean and shiny the surfaces become when cutting with a sharp edge tool, and the fine details that become possible with the hardness of these species. Recently, I have been introduced to Utile, which is an excellent and affordable substitute for Mahogany.
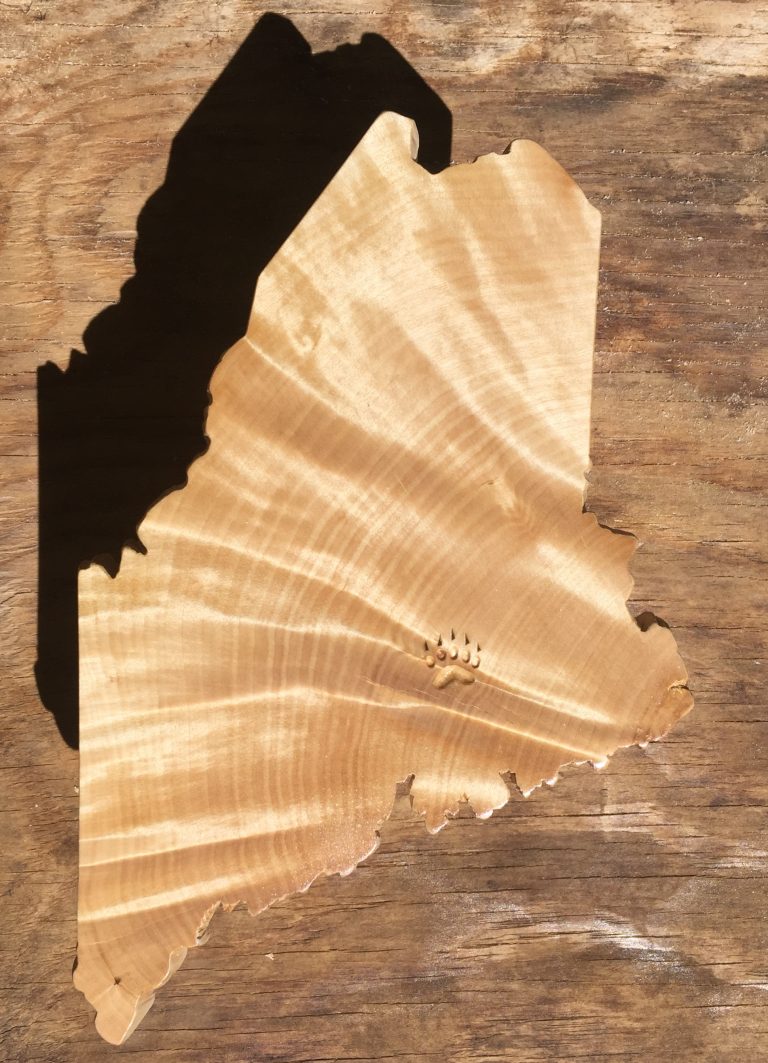
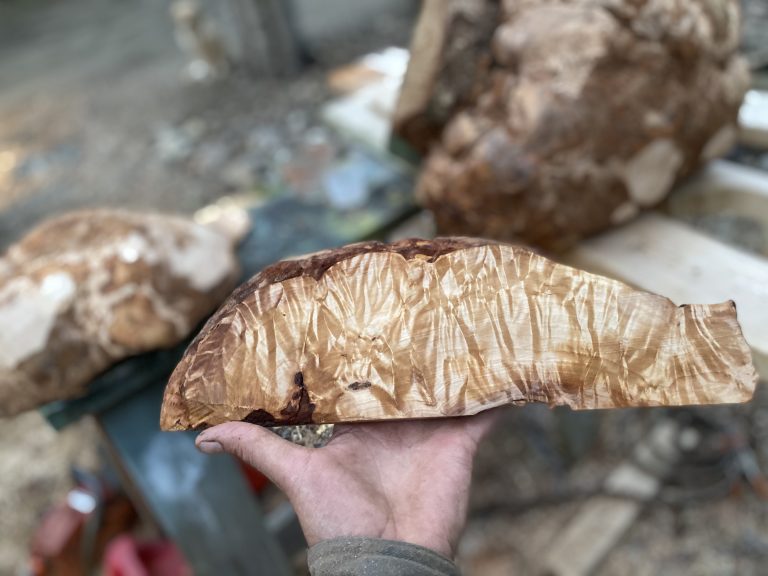
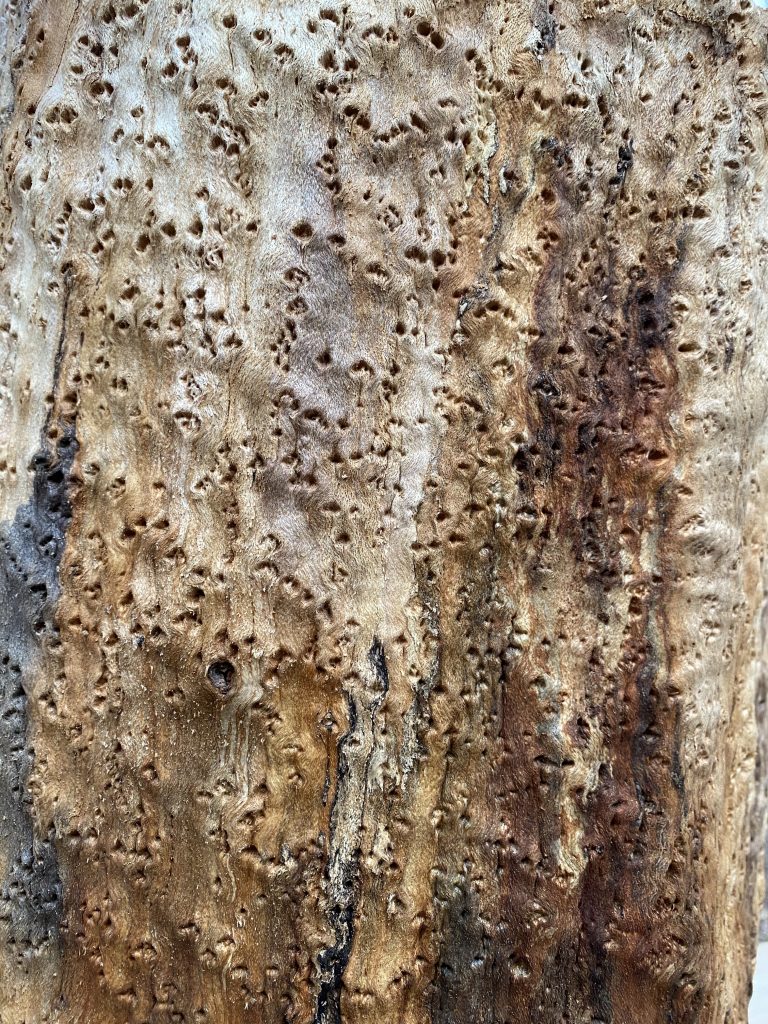
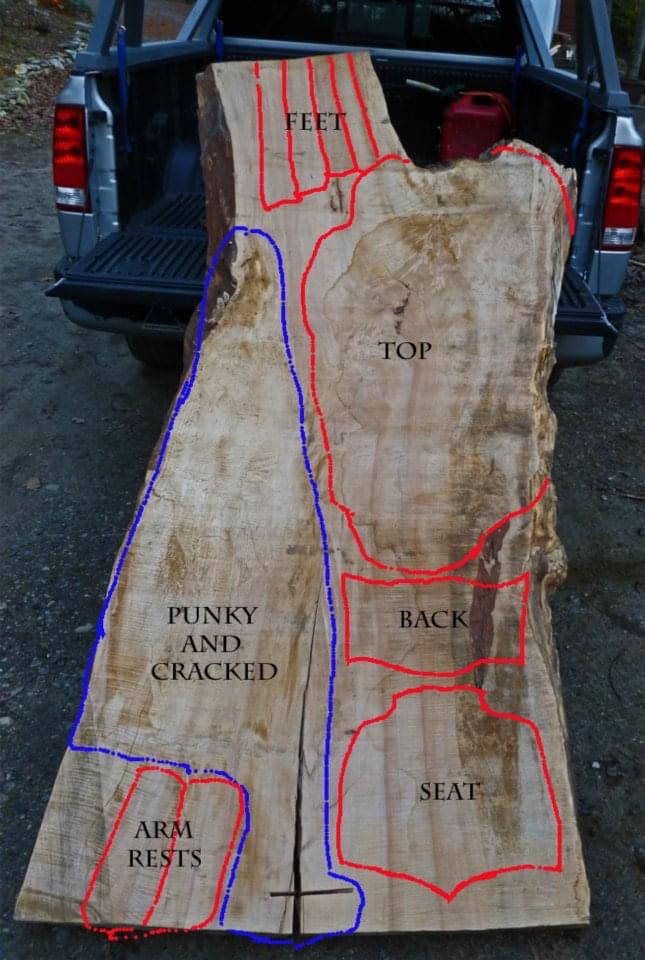
Question #6
Tobias: Please list your most used hand tools and tell us why they are your “go-to” tools.
Mark: I do have a favorite chisel, it is a 5/8′ firmer chisel marked “Buck” that I picked up at a yard sale for a Dollar. I always reach for it first from the drawer, as it seems to hold a sharp edge longer than the others.
For hand saws, I prefer the Japanese Ryoba style pull saws with both crosscut and rip edges. They are the easiest way to cut quick straight kerfs on small pieces.
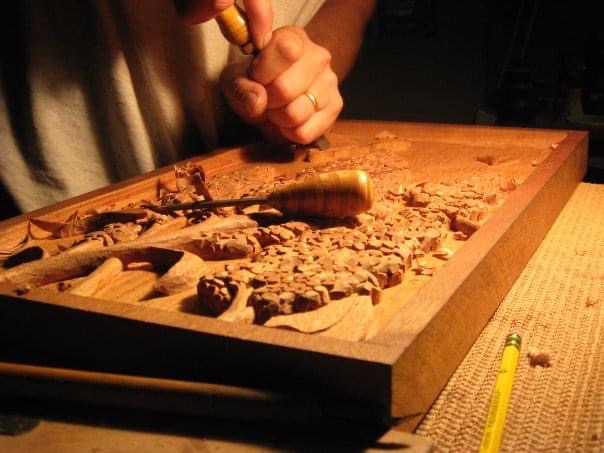
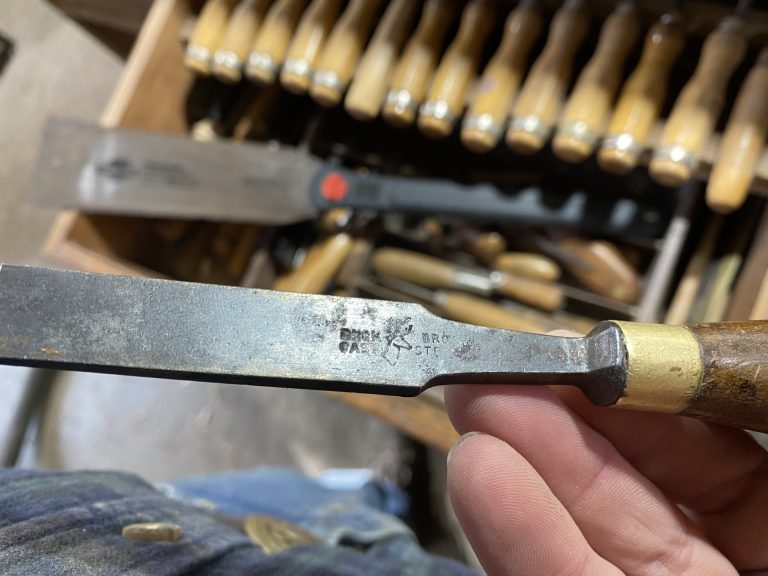
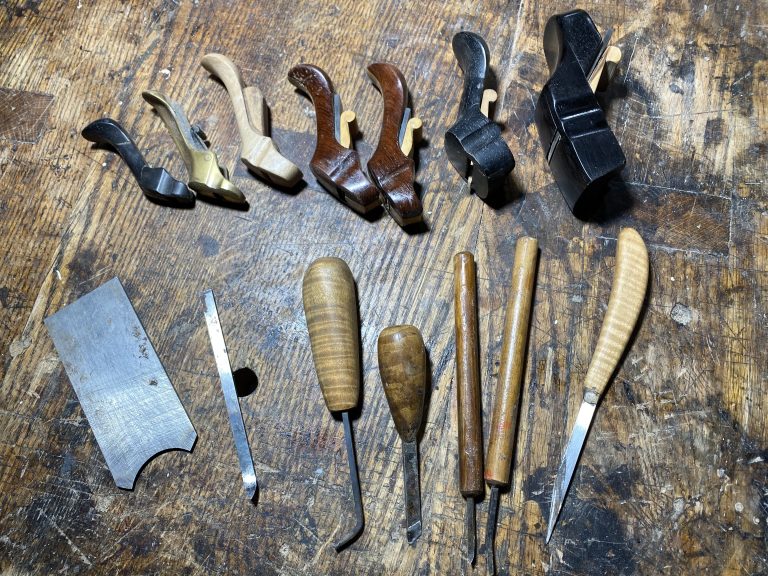
Question #7
Tobias: Can you list your favorite power tools and machines and tell us why?
Mark: My favorite stationary tool is my thicknessing drum sander, the Performax 16-32. It is perfect for achieving precise thicknesses of acoustic guitar backs, sides and tops. This machine also excels in getting a nice flat surface on figured woods that are prone to tear-out on the planer. The best use of this tool might be when levelling an inlay glued into the substrate. When I first got the Performax, I asked myself why I had not bought one years ago!
My favorite hand held power tool is a 4-1/2″ angle grinder. I have several of these tools, each fitted with a slightly different cutting wheel. One has chainsaw teeth, another has tungsten carbide burrs, another has rasp teeth and so on. These machines are the best way for me to produce a quick and controlled rough-out of any concave shape.
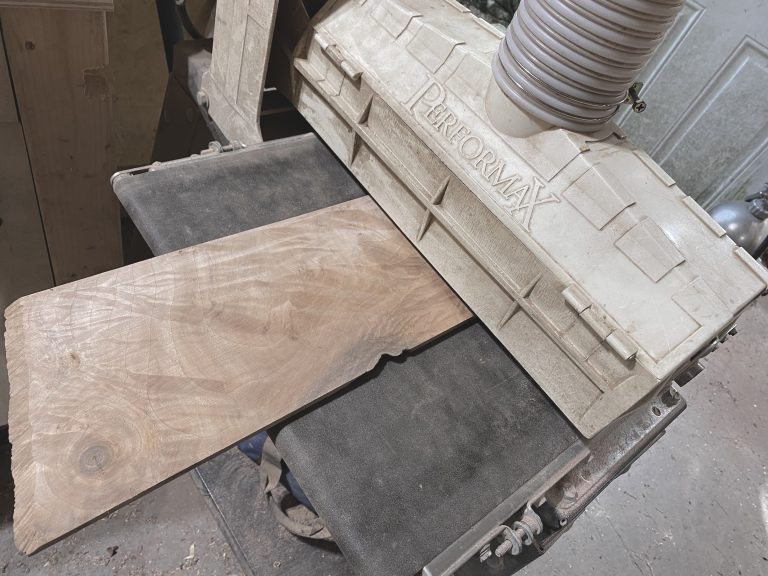
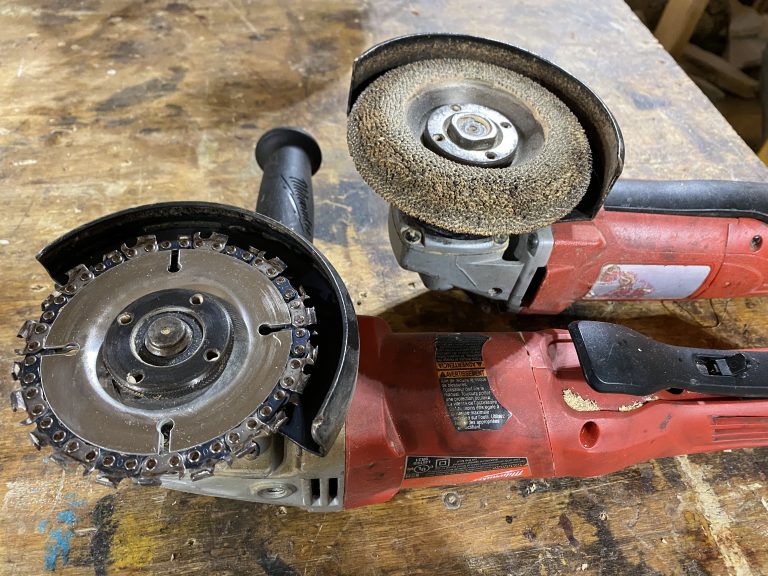
Question #8
Tobias: What is it about working with wood that you find most enjoyable?
Mark: I enjoy making things out of wood because it is already full of fascinating and beautiful character, very often unique to that single piece. When these features are showcased in the design, I feel like all of the hard work has already been accomplished! Nature is always producing masterpieces of art.
Often times with a really interesting piece of wood, I will study it for some time for it to tell me what form it should take, so as to make the best possible use of it.
My favorite moment, and I suspect most woodworkers might agree, is when the first coat of finish wets the grain and all is revealed!
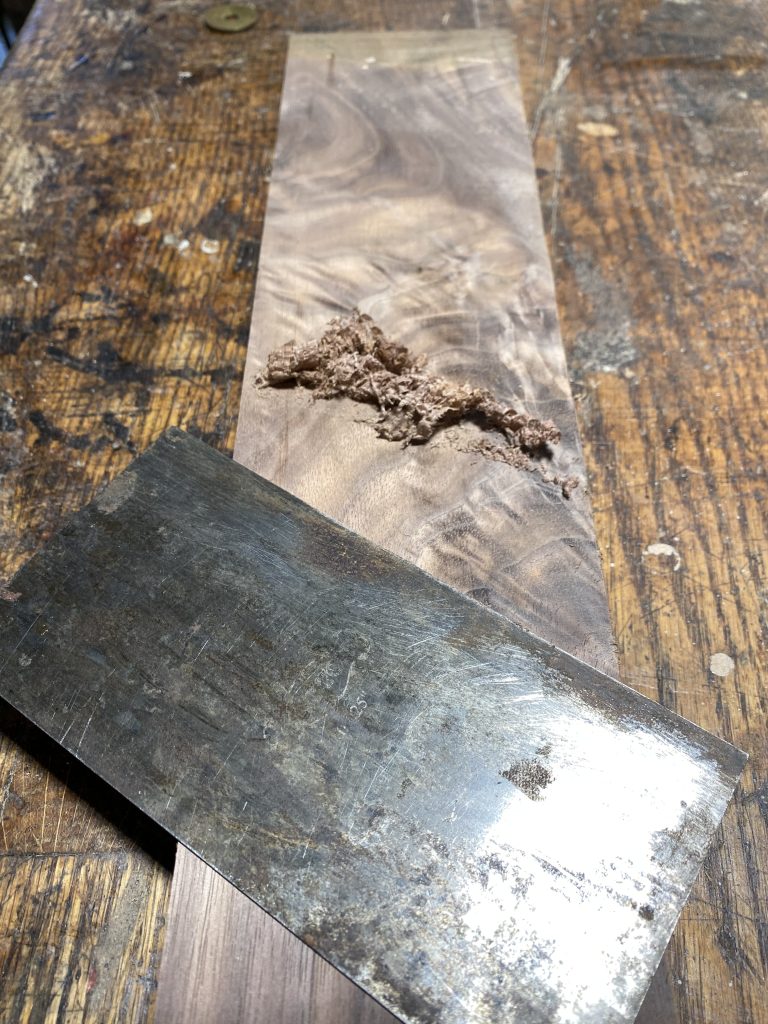
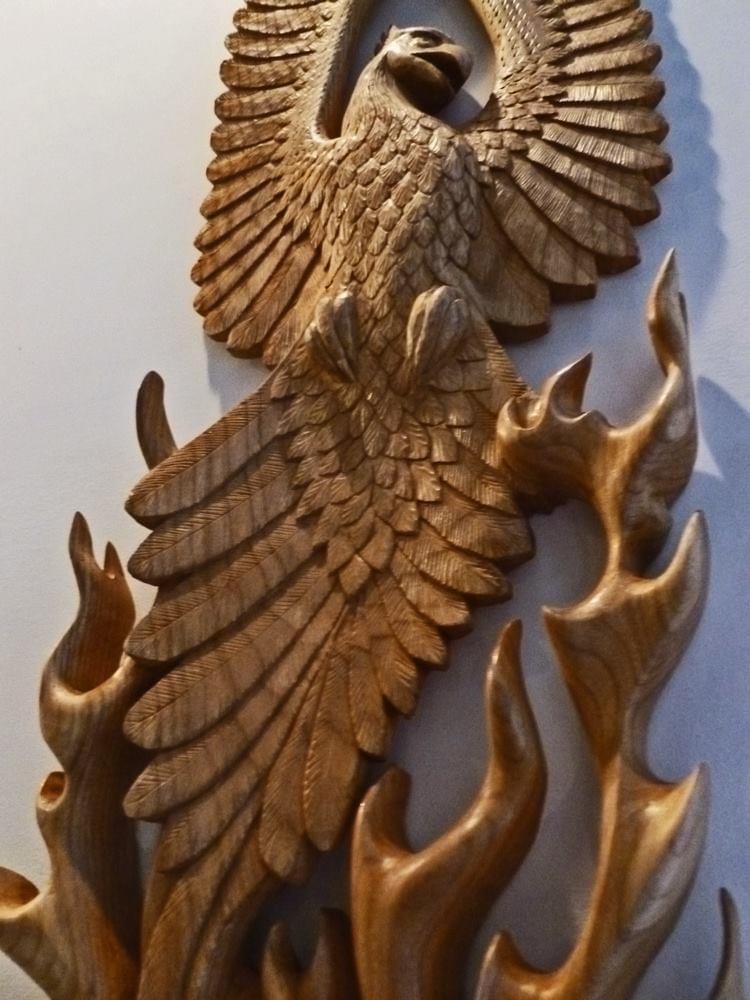
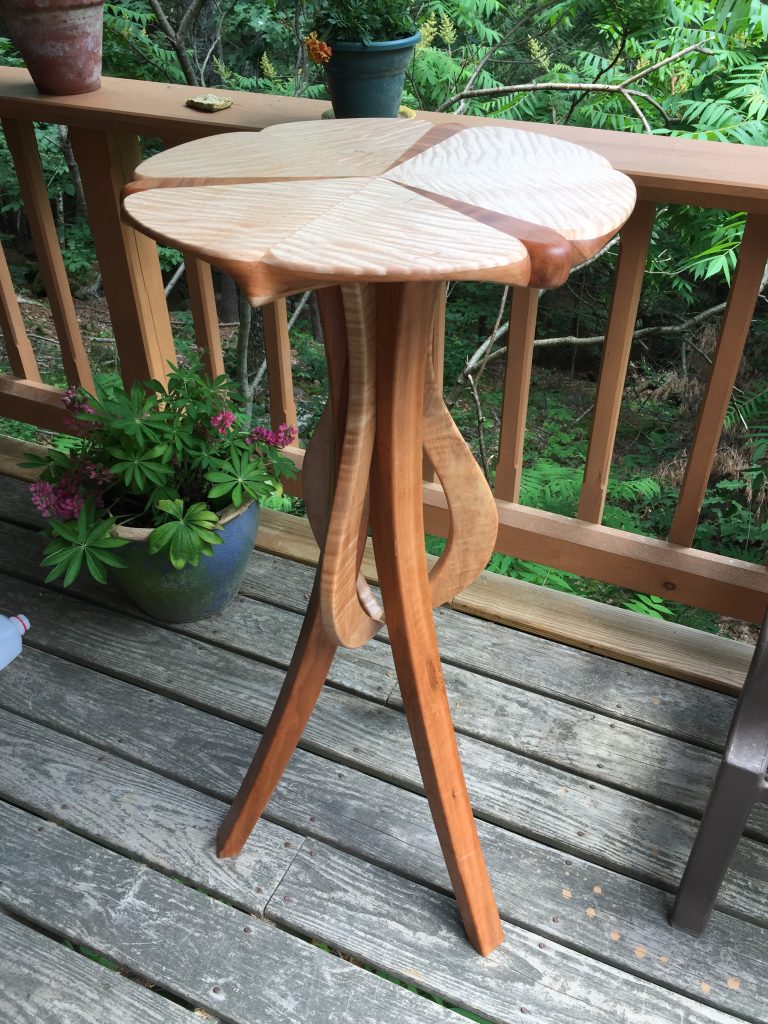
Question #9
Tobias: What type of workshop do you have, how has it evolved over time and why?
Mark: My shop is tiny by most standards. It is a 16′ x 24′ stand alone building with a loft space. My stationary machines are a table saw, jointer, drill press, bandsaw, portable planer and the drum sander. I have a dust collector with a chip shed just outside the building. I have one standing height workbench and a sitting height work area. There are also a propane heater and a wood burning stove for heating in the winter. The workshop is only a few hundred feet from my house, so the daily commute isn’t too bad!
I first set the building up as a workshop when I was making and repairing violins. It was the perfect size for that. However, I found that I needed to accept other work in order to offset the limited demand for newly handmade violins. This was naivety on my part, so that’s when I started doing furniture and cabinet commissions, which are readily available.
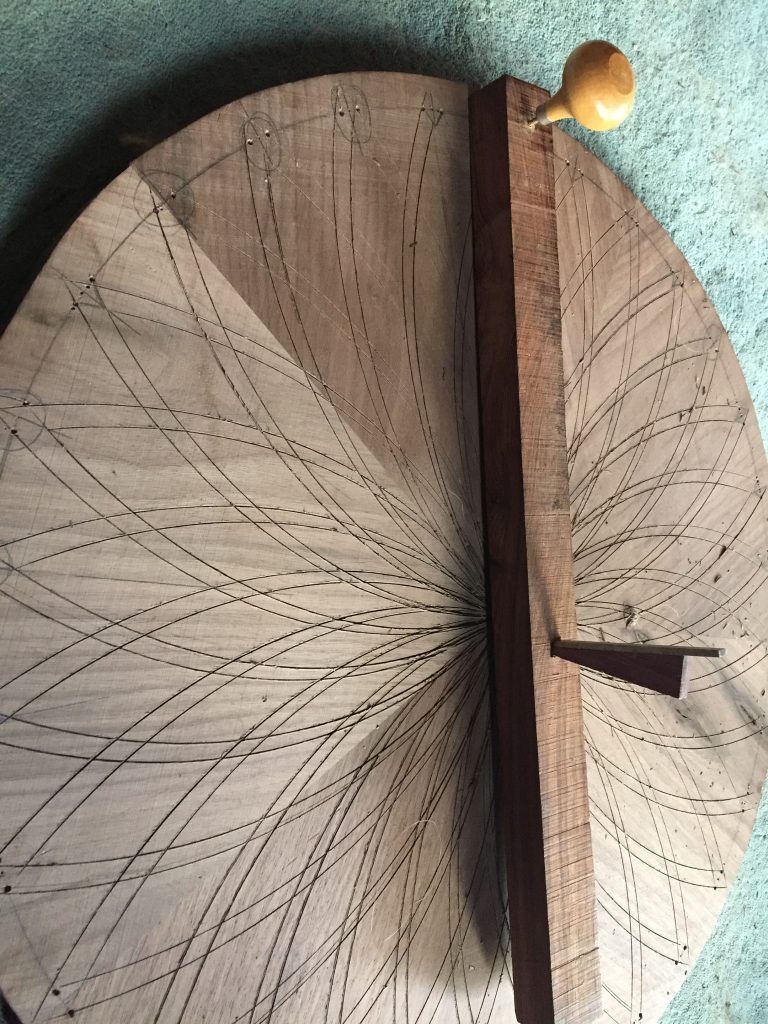
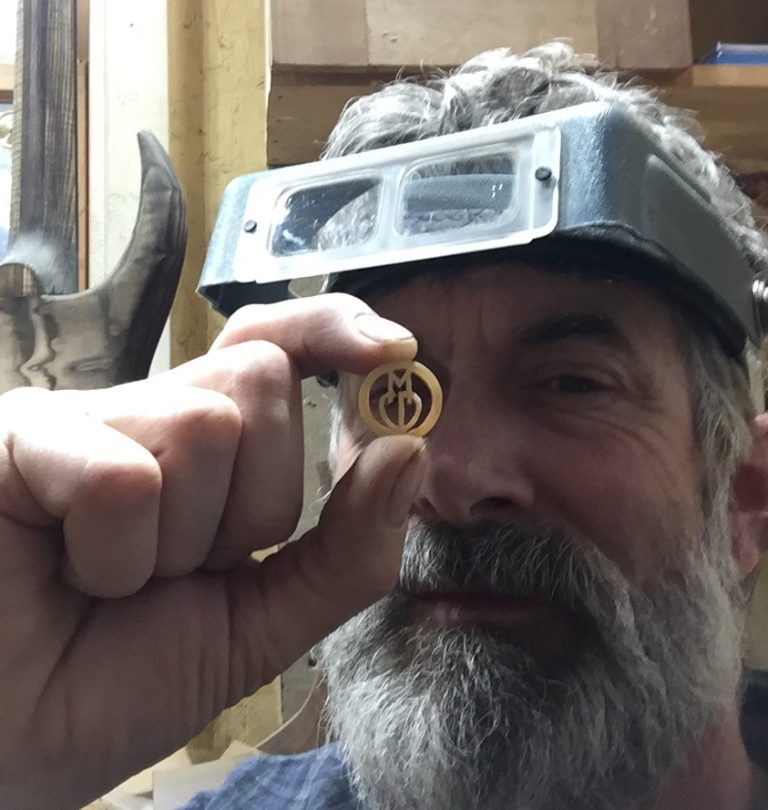

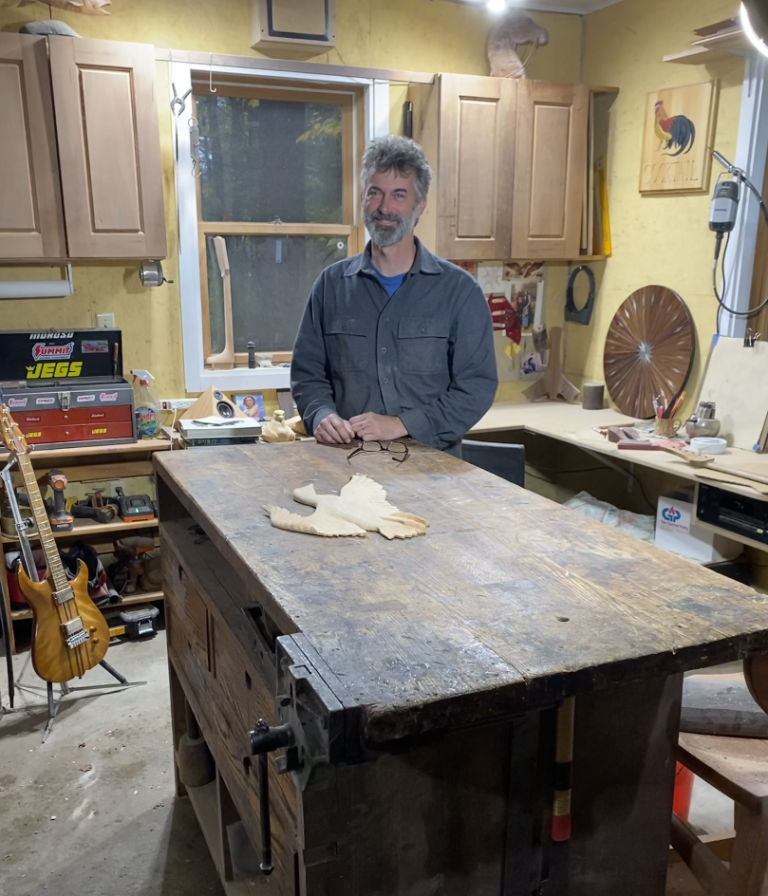
Question #10
Tobias: What is your clamp line-up and why?
Mark: I regularly use 36″ bar clamps for flat work such as table tops or drawers. I have an assortment of “C” clamps for laminations and `I use Jorgensen style wooden handscrews for holding jigs or patterns.
Recently, I acquired a vacuum bag and pump to use on curves and for veneering onto substrates. I also have a drawer full of rubber bands that are perfect for odd shapes when other clamping methods don’t work and no protective cauls are required to prevent dents.
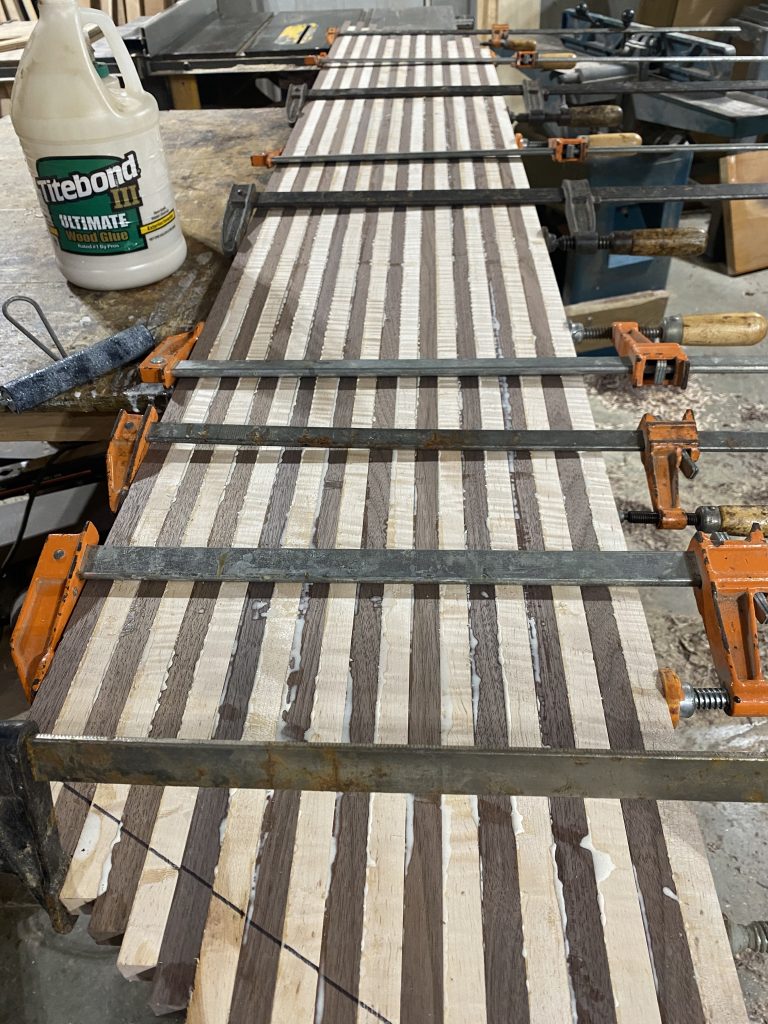
Question #11
Tobias: Which adhesives and glues do you use and why?
Mark: I use Titebond Type II or III adhesives in most situations, depending on whether the wood is dark or light. I also use traditional hide glue for my violins, as it can be “unglued” for repair and restoration work in the future. Modern adhesives are permanent and the joints are not repairable. This “reversible” property of hide glue is one of the reasons that there are 300 year old violins still in service today.
For odd or cross-grain laminations, I will sometimes use marine grade epoxy, which is great to fill gaps, seal porous grain and harden very soft woods. As well as the above, I make use of veneer adhesives that are specifically tailored to purpose.
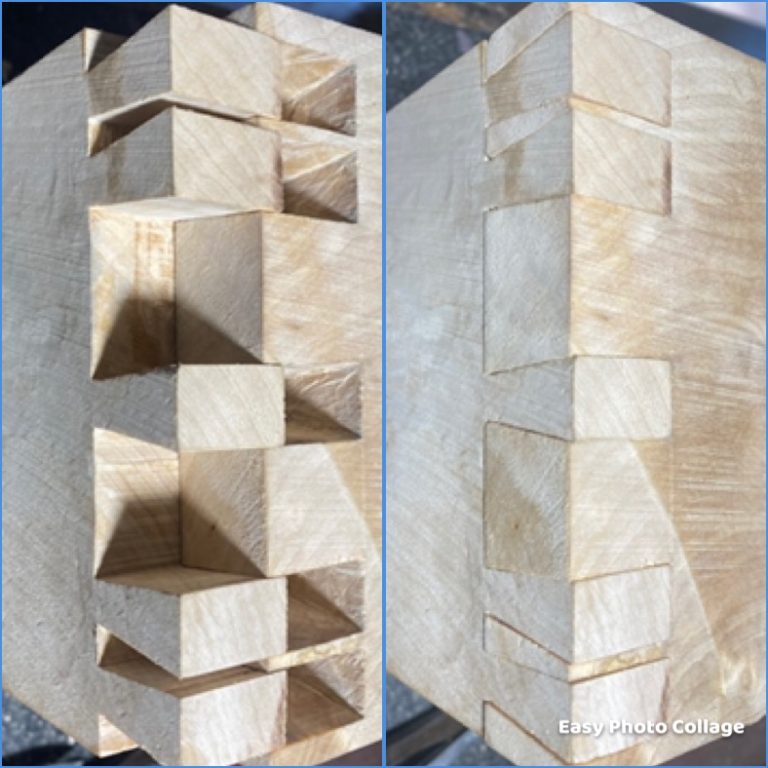
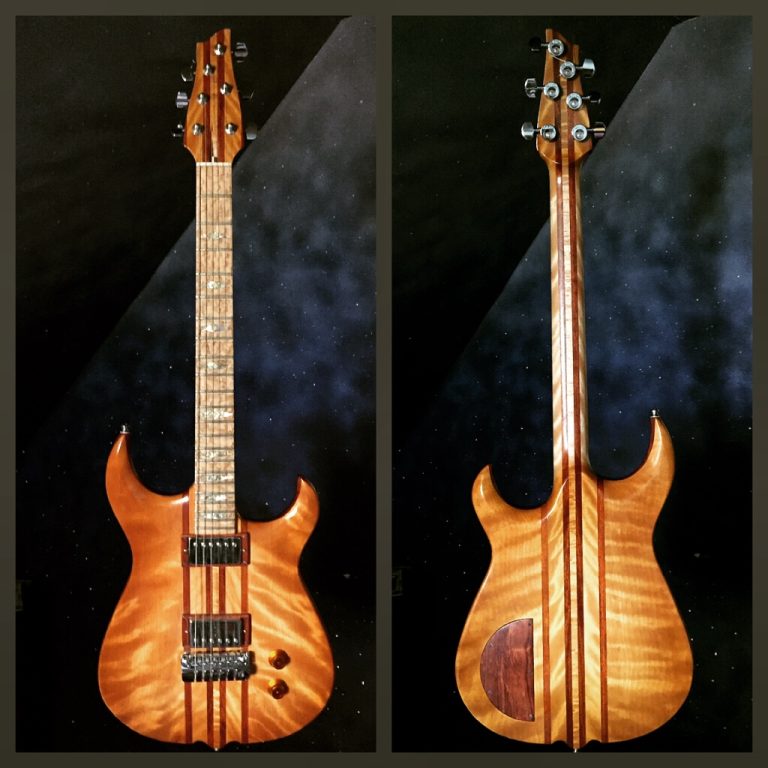
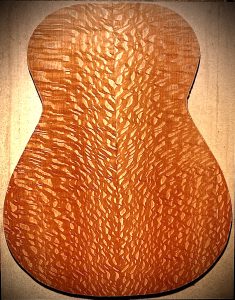
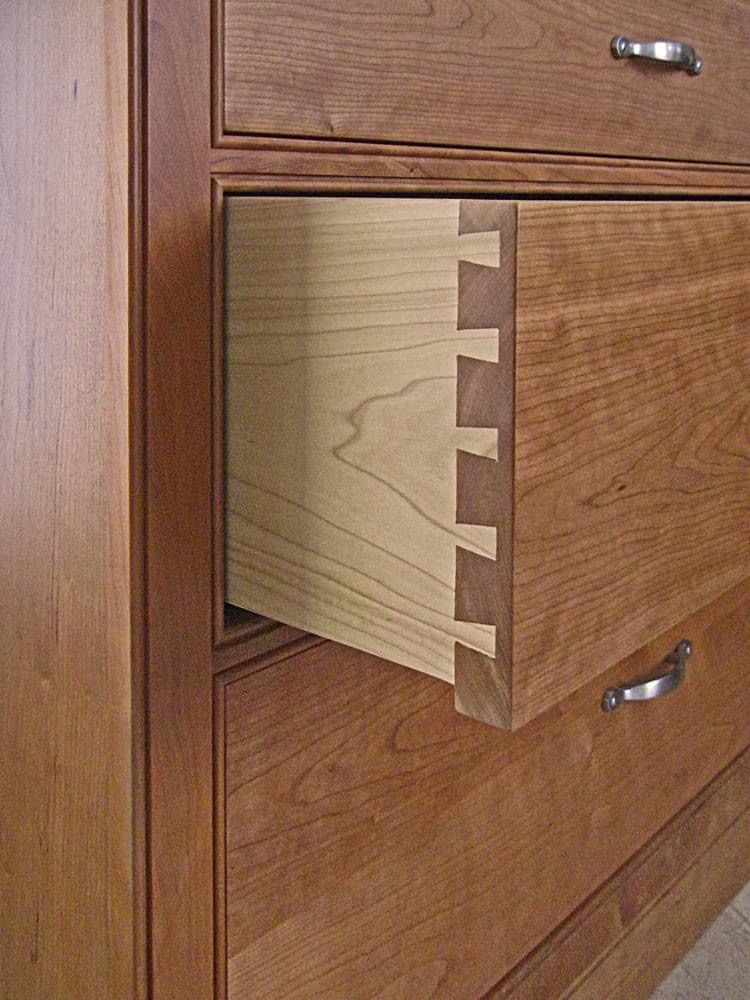
Question #12
Tobias: Which woods (exotic and local) have you not yet used and why are you interested in building with these species?
Mark: I have always loved the color and figure of the Redwood from California. It is often figured and I find it truly beautiful.
For exotic species, I love the orange color of Eucalyptus from Australia. I have seen guitars made from Pale Moon Ebony that are absolutely incredible! Either of those species would make an exquisite project!
I have a beautiful plank in my loft that I have been saving for the right occasion, no idea what species it is, so I can only guess. It might be Redheart or Bloodwood.
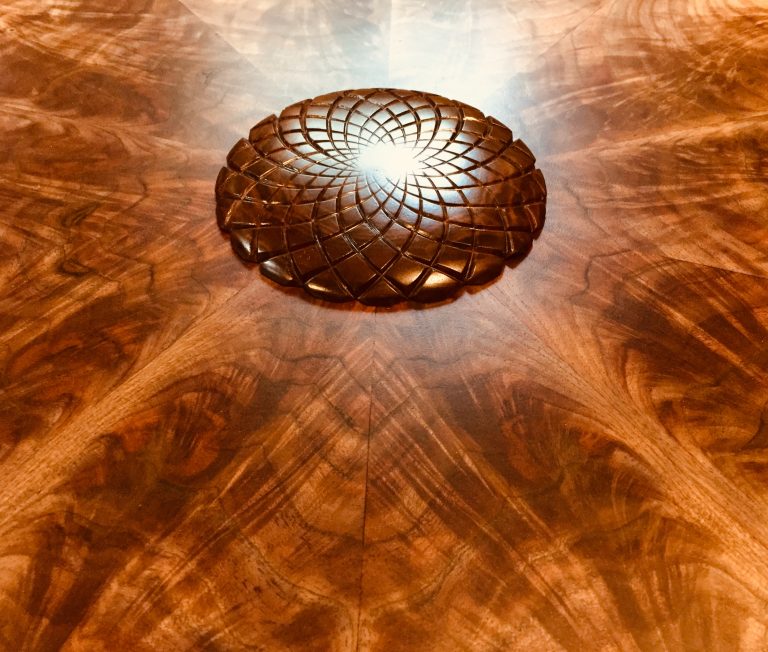
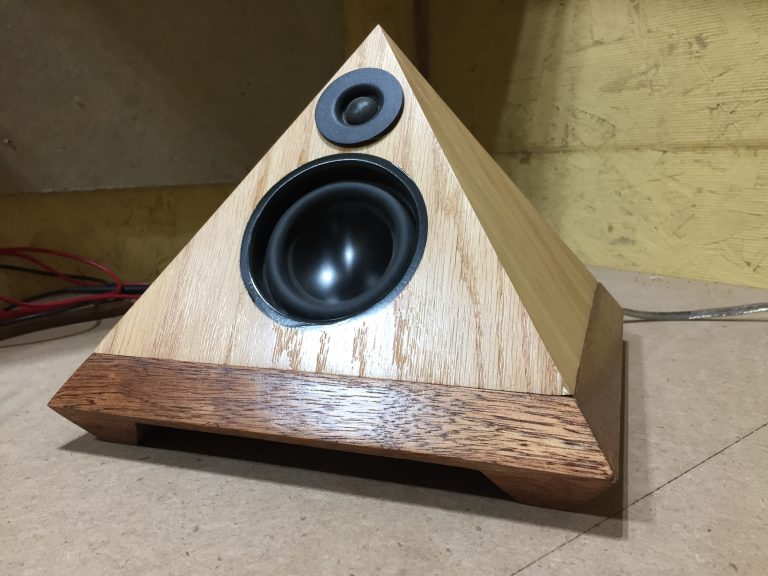
Question #13
Tobias: What and whom are your sources of inspiration for your craft?
Mark: I will often interview a client who is commissioning my work, to get to know them better. I really enjoy finding ways to make their piece personal, so the design can incorporate symbolism or details which they can relate to. Making something for a specific person or family is so much more rewarding than making something for its own sake.
Often, I turn to my memories of the mentors that I have been lucky enough to have and I ask them in my mind if a piece is really finished. It is a valuable exercise as it sometimes sends me back to a scratch or an errant curve that I had already moved on from. As I tried to explain earlier, often times I will get inspiration for a design from the wood itself.
I haave always admired Thomas Moser, a very successful furniture maker in Freeport , Maine. Another person who influences me is Larry Robinson, an exceptional inlay artist! The biggest influence and source of inspiration in my work has been that of both of my granmdfathers Jay Hanna and Olin Pankhurst. They were both immensely knowledgeable and helpful, but unfortunately they have passed on.
Jonathan Cooper is a violin maker near Sebago, Maine. He graciously guided me through the process of constructing my first few violins. I owe him much gratitude and I constantly work towards his example.
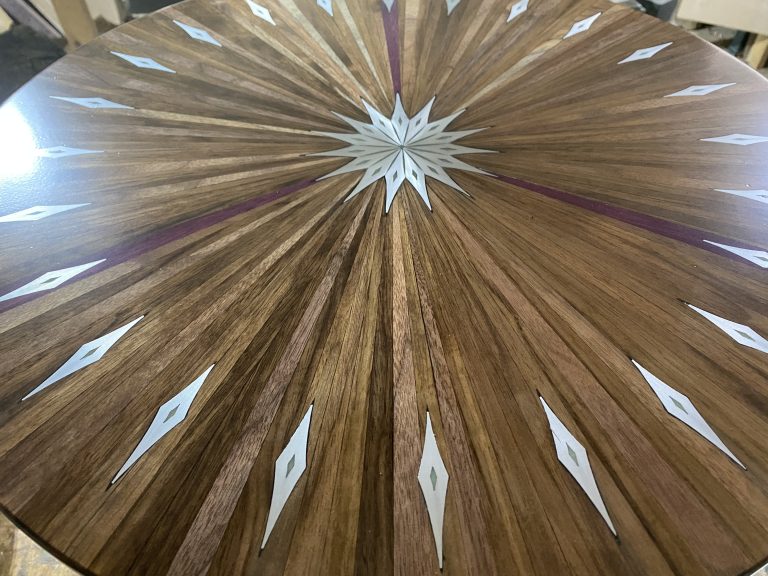
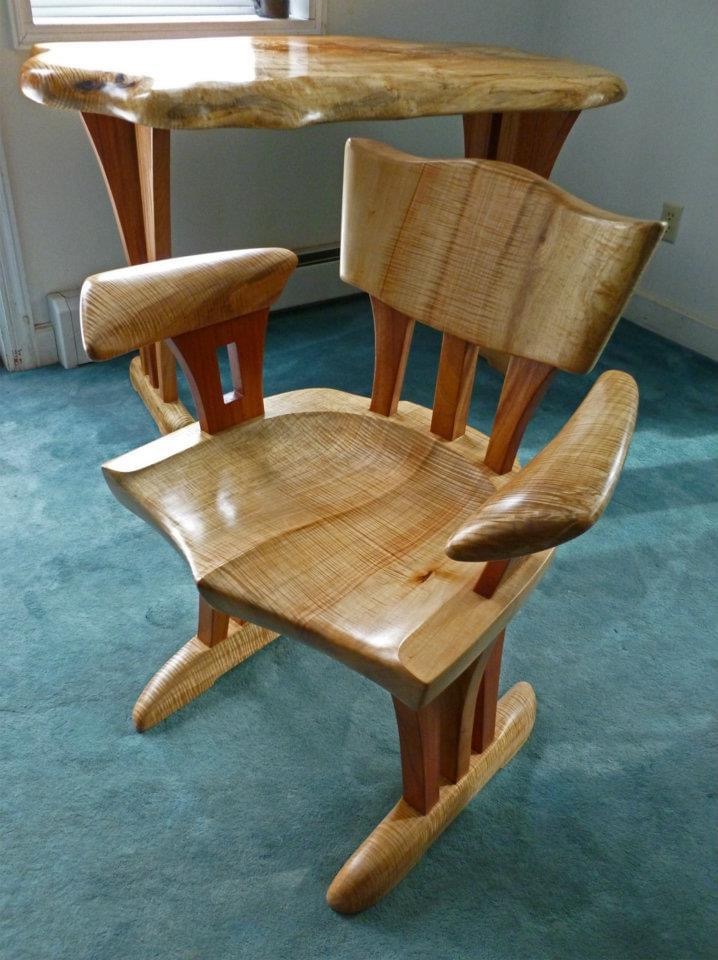
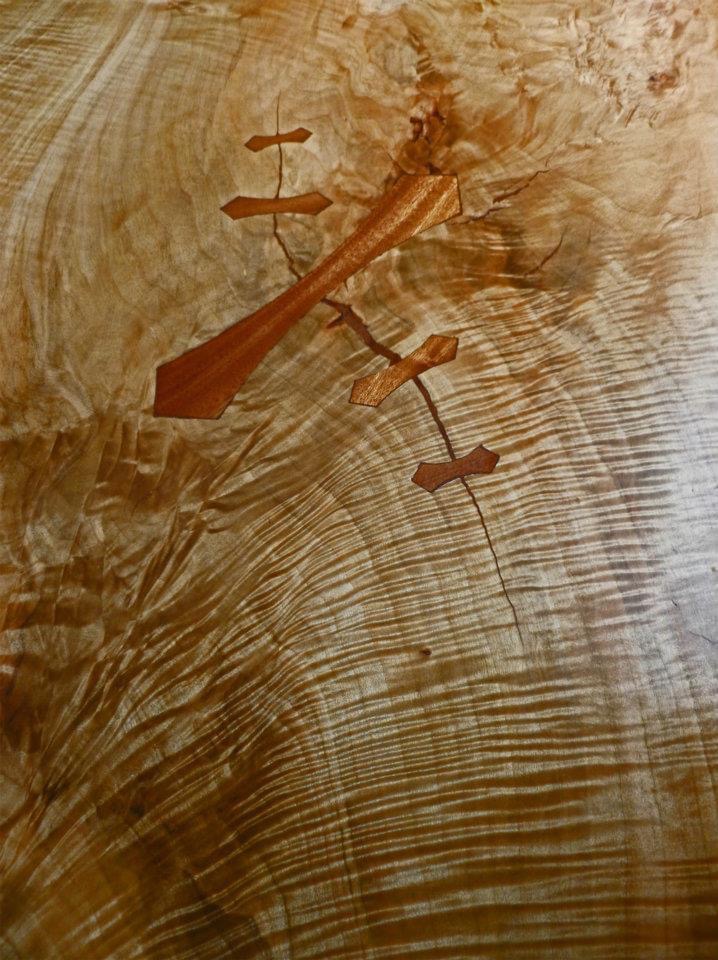
Question #14
Tobias: How do you design your pieces, Do you use CAD or SketchUp or do you draw out by hand?
Mark: Even though I have experience with computers and programs, I much prefer to draw with pencil and paper. I have numerous sketch books filled with random ideas, shapes and patterns. These pads are a kind of visual journey for me, and I find that I have to sketch in order to not forget a moment of clarity. I also have other notebooks that I use to expand ideas for current projects.
There are times when I think that investing in current technology would allow for more professional looking proposals, but there is something satisfying to me about a quality, hand drawn perspective to present to a client.
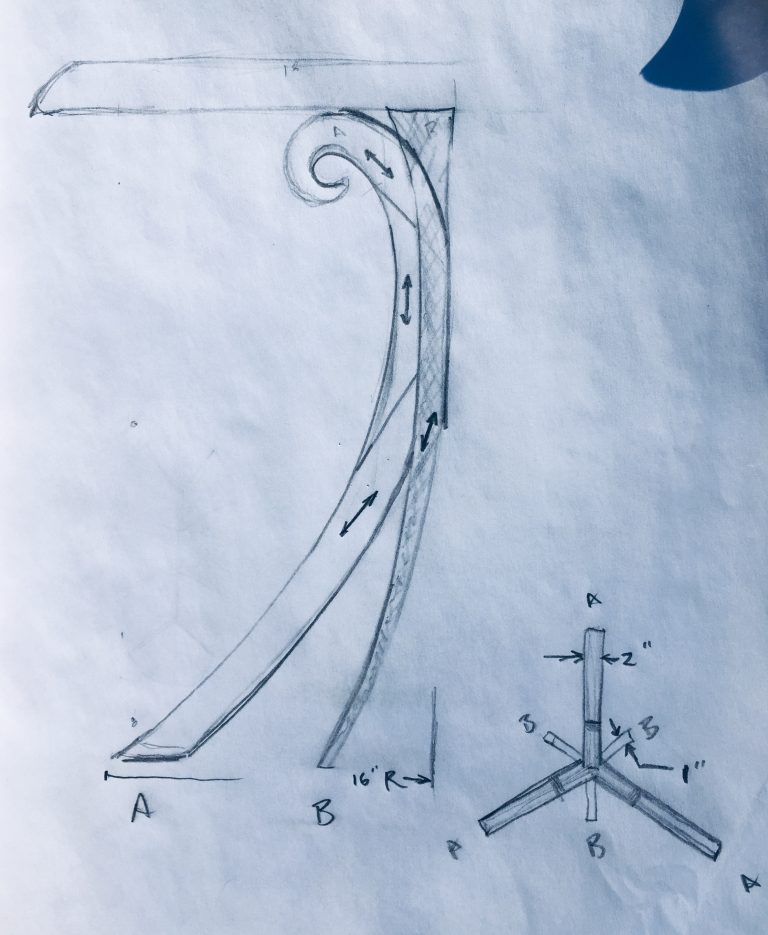
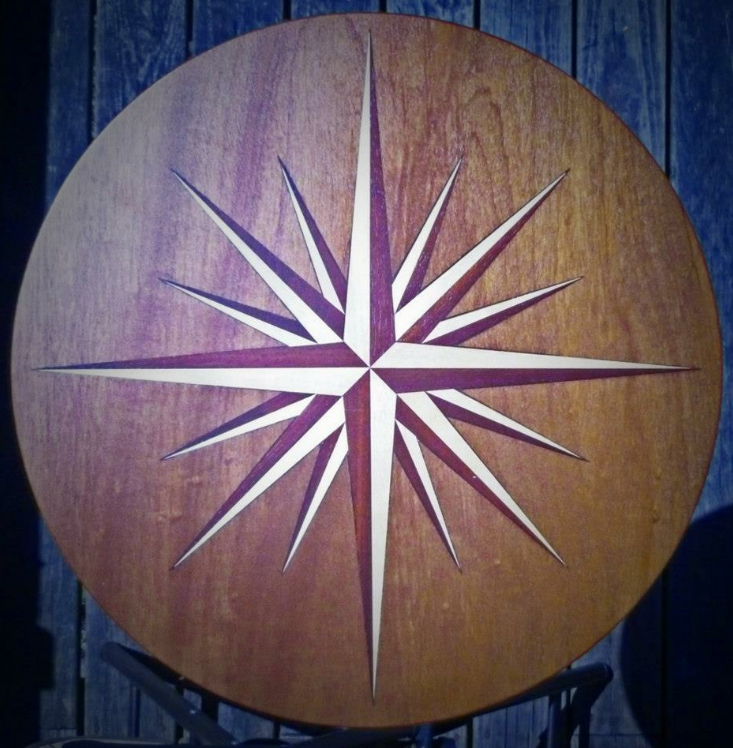
Question #15
Tobias: What are your finishing regimes, what products do you use and which are your favorite processes?
Mark: My favorite finish involves polishing a hardwood until the surface is as clear as possible. This is a tedious process. I used to fool myself that the finish will cover up whatever scratches and marks I had left on the piece. The reality is that this incorrect assumption only serves to preserve poor workmanship for all to see! Removing a finish to get to a scratch is a ridicluous waste of time, so I very quickly learned to be patient and attentive when inspecting a surface. Direct, raking sunlight is the very best way to locate areas that require more attention. When the piece looks great in this light, it will look great in every other environment.
A light tung oil or other similar penetrating oil finish will wet the grain and harden below the surface. I like being able to control gloss by the number of coats that are applied. I also like this type of finish because it will still feel like wood, unlike the result that is created by film finishes. I only use urethane varnish or catalyzed lacquer when absolutely necessary.
Violins require specific and traditional oil or spirit varnish, applied with a quality brush. My acoustic guitars are finished with nitrocellulose lacquer which is sprayed on with my HVLP spray gun.
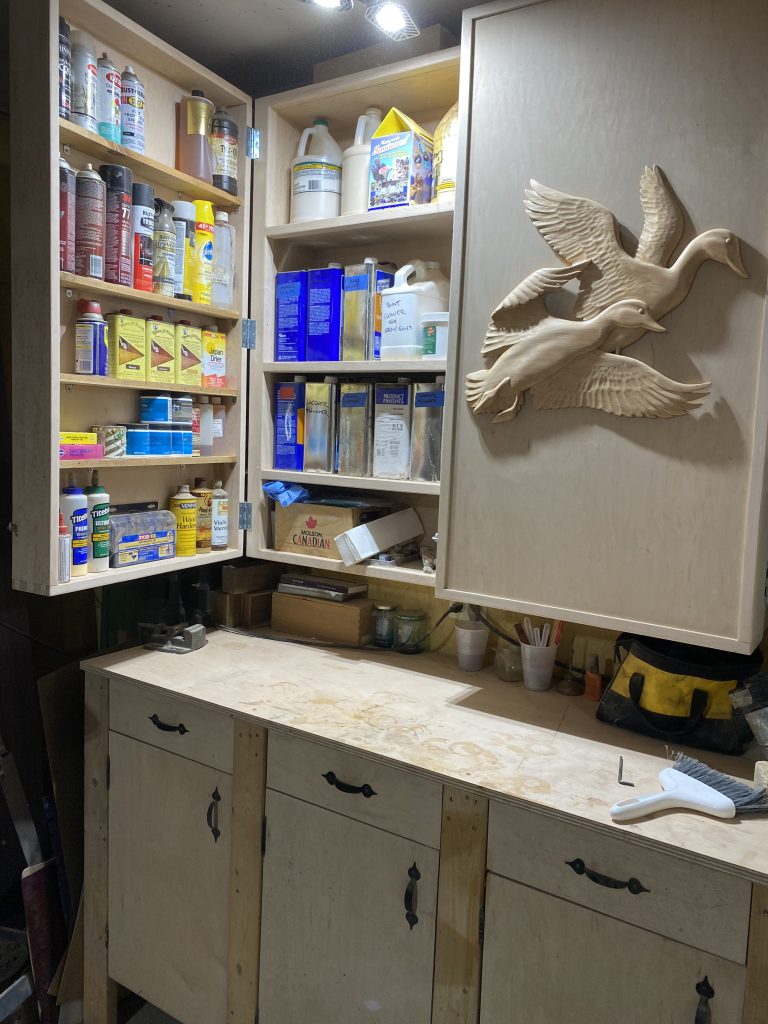
Question #16
Tobias: Which parts of working with wood do you dislike the most?
Mark: Sanding! It is necessary in most projects, but I try my best to keep it to a minimum. If I can, I use a card scraper in conjunction with sanding. Even though it requires an extra step of maintaining the burr on the scraper, I find that it is most often better than sanding. If I do use a palm sander, I follow up with a card scraper. The scraper not only levels the surface of the wood, it slightly burnishes as it cuts, which I consider to be a desirable result. Scraping produces fine shavings instead of fine dust that coats every surface in the shop. When I have to sand, I try to do it outside if the weather is nice.
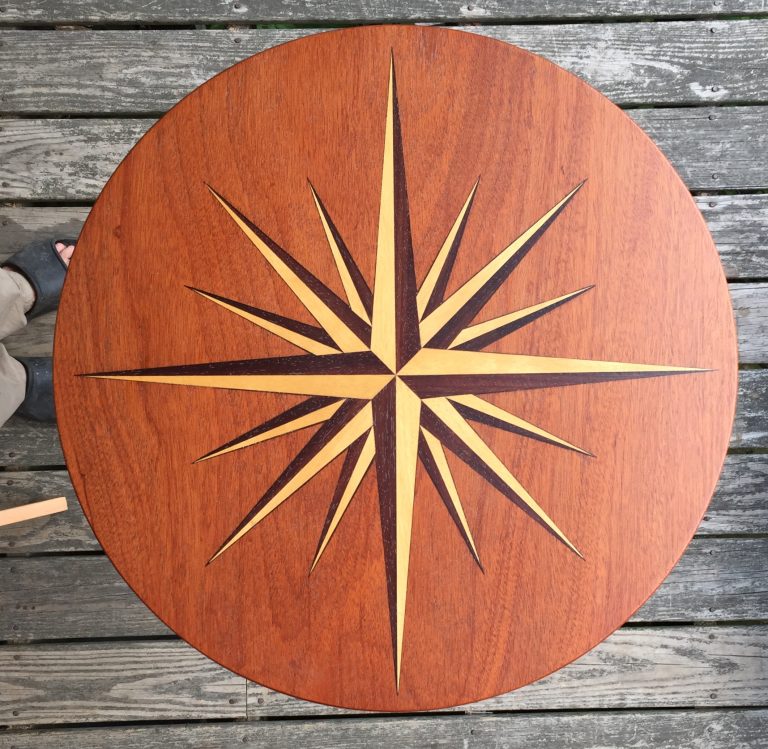
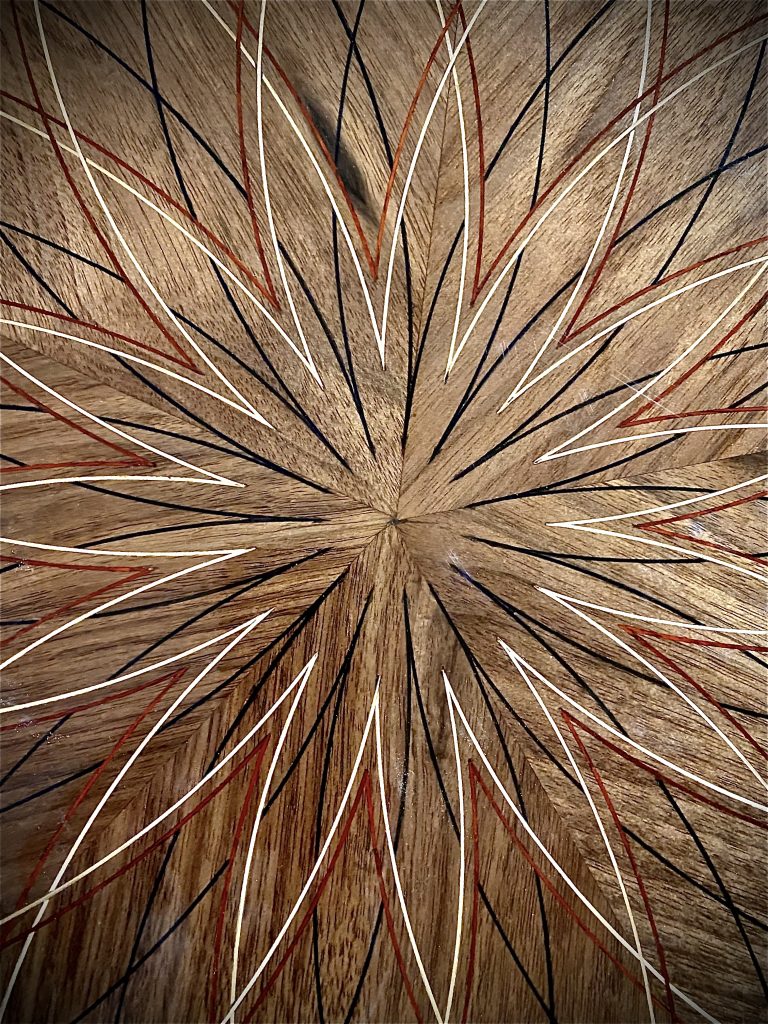
Question #17
Tobias: What is your favorite music to listen to whilst working in your shop?
Mark: When I need to work out a design with specific requirements or verify detailed measurements, or even use power tools where concentration is required for safety, I prefer the shop to be quiet with no distractions. This includes my dogs who always want me to throw balls for them.
When it comes to hand tool work or doing repetitive and tedious tasks, I find that guitar oriented rock is the music genre that helps me the most. That said, I can also equally enjoy a violin concerto or an acoustic guitar instrumental.
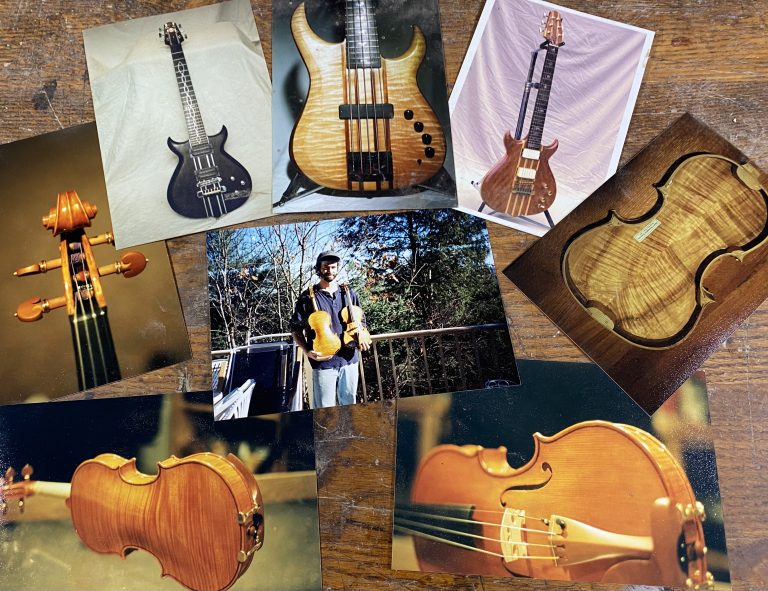
Question #18
Tobias: What is you tool sharpening regime?
Mark: Like all of us, I prefer sharp tools. I was taught that a dull cutting tool is a dangerous tool. I really don’t have any dedicated sharpening machines, just a few low-tech methods.
I touch up the edges of my hand tools on a 2″ diamond plate as soon as they start to show any streaks in the cut or if I notice myself having to force the tool. When I can no longer get the tool sharp with the diamond plate, I bring it to the bench grinder, where I put a hollow in the bevel just up to, but not into the cutting edge. It then goes to a series of abrasive sheets stuck to a piece of granite countertop. A few swipes restores the cutting edge. Finally, I retiurn to diamond plate to polish the edge.
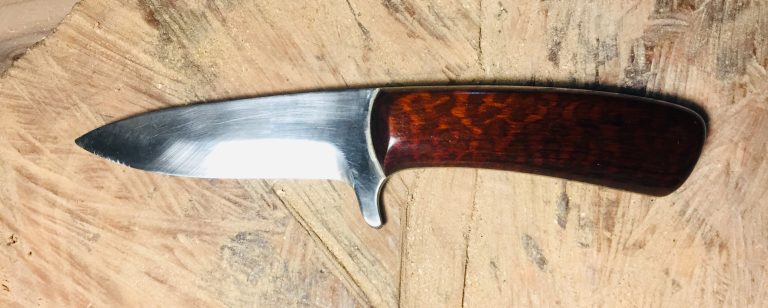
Question #19
Tobias: What custom jigs or tools have you developed for your woodworking?
Mark: I have several table saw sleds: one for cutting tenons vertically, one for cutting equilateral triangles for my pyramid speakers and one for cutting fretboards with scale templates for guitars and basses. I also have a number of distance and angle gauges that I use to determine the geometry of chair stretchers, as these are never straight forward. For router work, I have several guides and fences thqat I attach to my small handheld router to limit the size of the cut.
When laying out any curve that needs to be repeated more than twice, I take the time to make a pattern and then use it to repeat the shape. This also applies to dovetails. Instead of laying out each corner, I make a template of the tails that I want over the width of the board, so that I only need to do the layout once. I now have a drawer full of templates for dovetails that I can use whenever appropriate.
I also have a variety of odd shaped knives and scrapers that I have made to fill various requirements. The best tool that I have developed is my luthier’s hollowing plane. I made the first one a long time ago to replace an industry standard brass finger plane that I found was uncomfortable to use and the shavings could not properly exit the tool with my finger in the way. I have since made a jig to reproduce my planes and have sold hundreds of them on Ebay over the years. I continue to make the little planes in small batches from time to time.
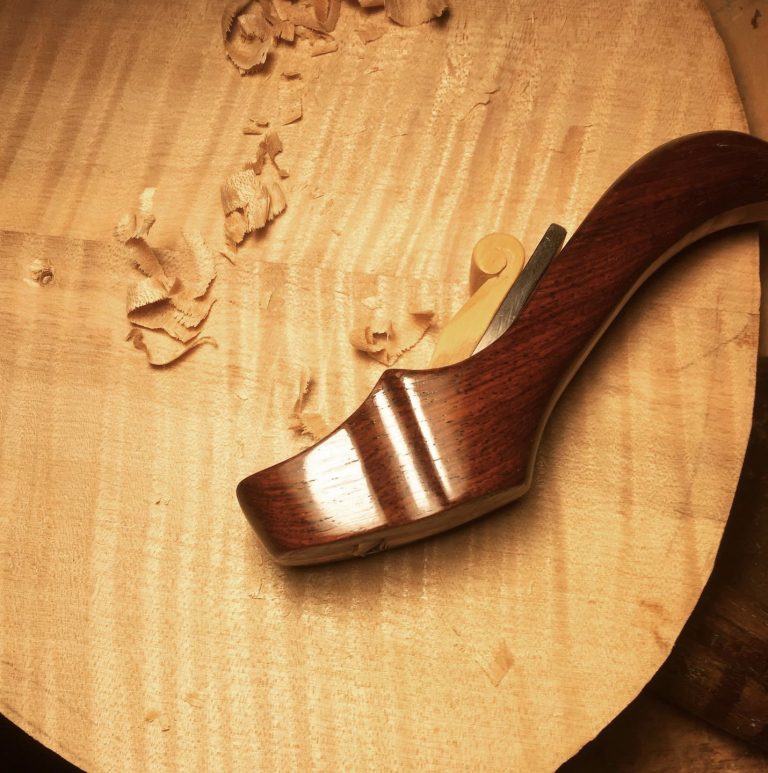
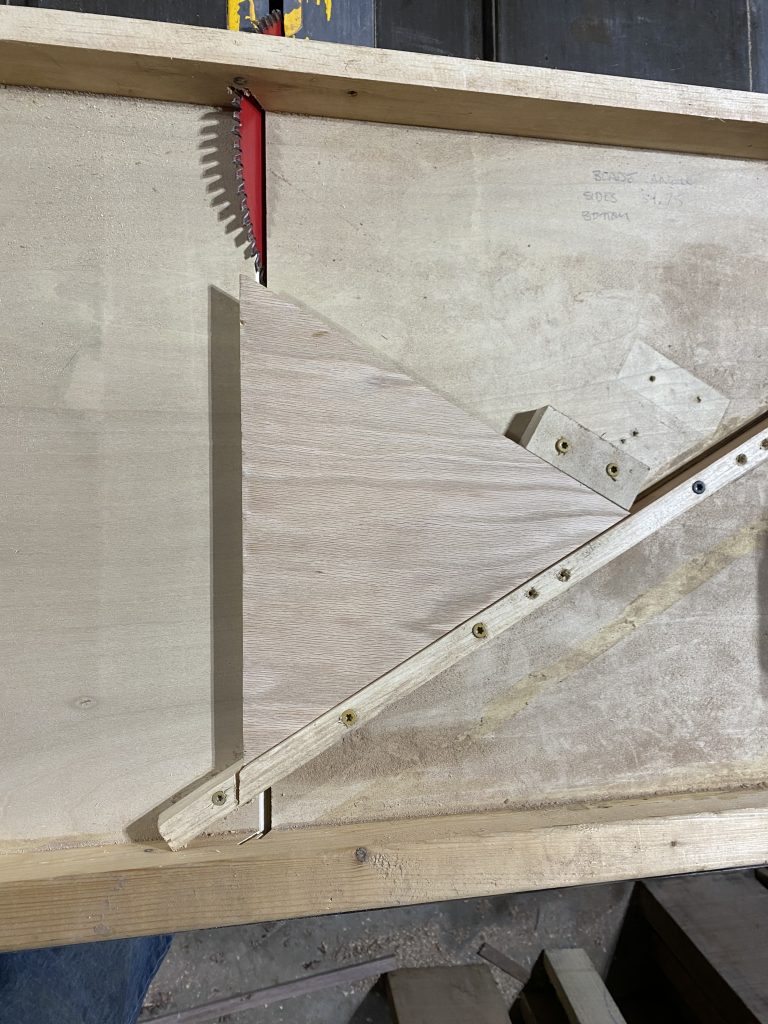
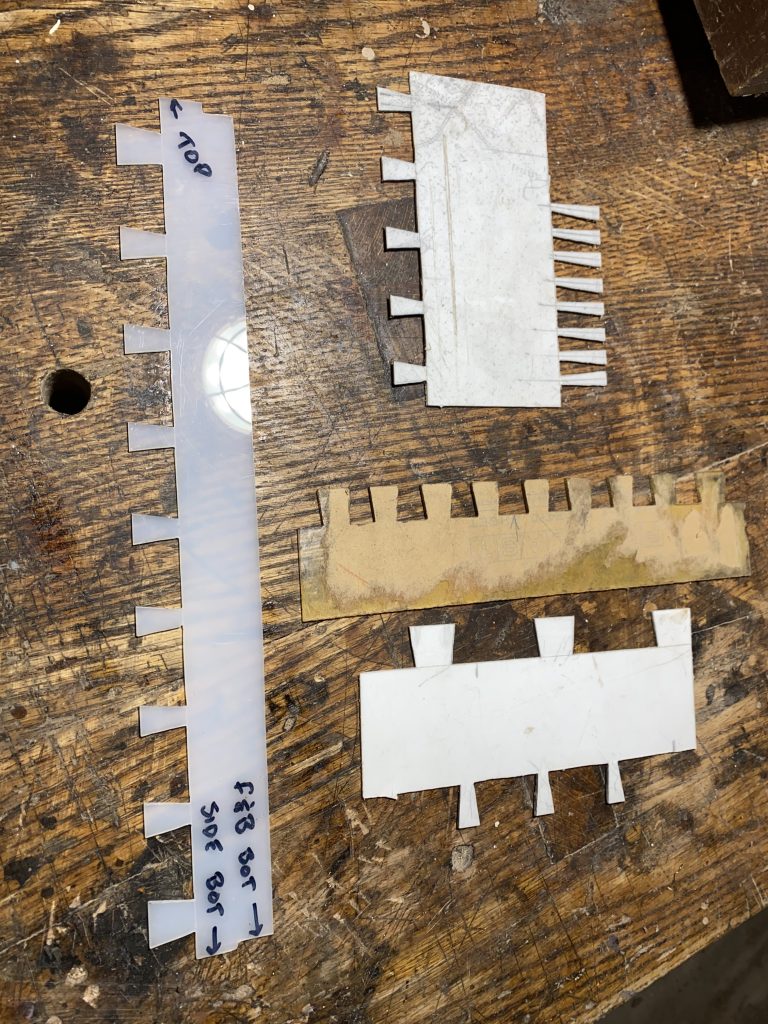
Question #20
Tobias: What is the next piece you are going to build and why?
Mark: One of my bad habits is to allow inspiration for a new project to interfere with my current work, meaning that I may start a new project in my mind, before finishing the one in front of me! I confess to resawing a nice piece of lacewood I received from a friend, while working on a cabinet job. I had pictured this Lacewood (which was perfectly quartersawn), as a guitar back and sides, so I cut it up accordingly. Then the compulsion was to joint the back (actually I made two and a neck to match)…
I am now looking forward to getting the cabinets finished and delivered so that I can continue with the guitar!
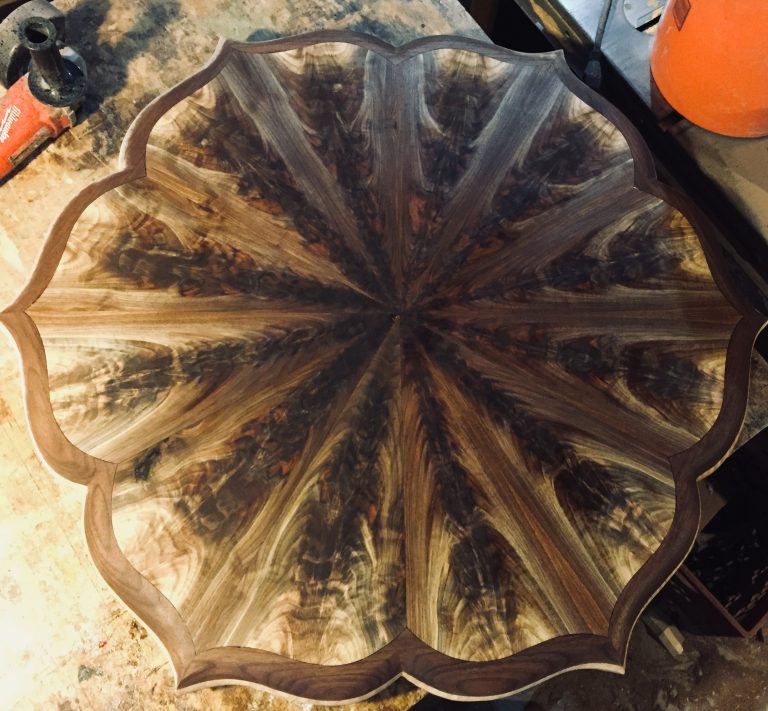
Tool Wishlist
- I need a new Planer! I have a 20 year old portable, that I have repaired several times. Maybe a helical head machine will be the way to go.
- I find that I do need a larger bandsaw.
- As long as I am dreaming… I would also say that I have always wanted a sawmill next to my shop. I have said “no” to far too many free logs in the past.
Lumber Wishlist
I have been collecting wood for 30+ years and can say that I might well have more than I can use. The loft above my shop is full of my “someday” boards! I still always will bring something home if it “speaks to me”.
I would love to find some Redwood from out West, or some “sinker” hardwood from the Great Lakes.
Makers with whom I would love to spend quality time
- Thomas Moser
- Lary Robinson
- Jonathan Cooper
Links
Email: mcdonovanwoodwork@gmail.com
Instagram: @mcdguitars
Instagram: @donovansbench
Facebook: @mcd.finewoodworking
My late grandfather’s book: ISBN # 0-937822-14-0 The Shipcarver’s Handbook by Jay S. Hanna
Our sincere thanks to Mark for sharing his woodworking journey with us. We are sure that he will become an inspiration to many others.
Please remember, if you know of any woodworkers who are doing great work, yet are hiding away in their shops, please let us know at info@rarewoodsusa.com
Awesome interview! Beautiful pieces! Thanks so much for sharing!!
Very interesting interview! If you buy a saw mill buy a wood mizer or find some one in your area that has one that dose custom sawing at your house .
These wood working stories, are truly incredible, I’ve been in building since I was fifteen , worked on a lot of high end jobs. These people you interviewed are truly on another level great stuff . I am now 65 and slowing down, building my last house, and hopefully will try some interesting things with wood , truly inspired, keep the interviews going . Thanks Thomas Frost . Rangeley Maine .
Another great read. Friday night highlight for me.
I loved reading this and learning the process of Mark’s woodworking brain! He is so talented and I love the pieces shared here especially the doors! I hope your woodworking wishes come true, Mark!
Excellent and versatile craftsmanship & craftsman; thoroughly enjoyed viewing all your work and pieces! Drive on, Mark! John Willette